鋳造方案設計は、不良品を発生させずに目的とする製品を製作するのに、重要な役割を担っています。こちらの記事では、その鋳造方案の概要と手順についてご紹介いたします。
鋳造方案とは
鋳造方案とは、高温で流動性のある溶湯を鋳型に流し込み、鋳型内部で凝固・収縮していく過程で欠陥を発生させることなく、目的とする製品を完成させるために、鋳造に関わる各要素について企画・設計を行うことです。
鋳造方案設計の手順
1:製品形状の決定
ダイカストの生産性の80%が製品形状と鋳造方案で決まると言われるほど重要な工程です。製品の機能を損なわない範囲でダイカストしやすい製品形状・製品規格を決定します。
2:使用ダイカストマシンの決定
製品鋳造に必要な型開力・型締力を有しており、ダイカストマシンの仕様に即した最大鋳造質量や金型厚さの範囲内であることを確認し、使用するダイカストマシンを決定します。
3:金型分割面の決定
製品形状のどの部分を固定型、可動型、中子等で形成するかを決定します。
4:金型レイアウトの決定(製品配置、ゲート位置の仮決定)
製品形状の分割された部分を固定型、可動型、中子のどこで構成するかのように、製品形状を金型の中にどの様に配置するかを決定します。「金型分割面の決定」と並行して決定されます。
5:工法の選択
製品形状、要求機能、品質基準などの条件により普通ダイカスト法では対応が難しい場合があります。特殊ダイカスト法を採用、もしくは普通ダイカスト法と組み合わせるのかなどを決定します。
6:プランジャーチップ径の決定
鋳造圧力、スリーブ充填率、ゲート切替高速区分について検証し、それらに対応したプランジャーチップ径を決定します。3項目のいずれかの基準を満たせない場合は、製品機能から優先順位を決め、優先順位の低い項目を基準範囲から外すなどして決定します。
7:鋳込み中心と製品中心位置の決定
金型の型締め時の剛性や金型サイズ、ランナーのレイアウトによって決定します。
8:ゲート断面積の決定
ゲート断面積はゲート速度との関係により決定されます。推奨ゲート速度は30~60m/sとあり、一般的な製品については40m/sぐらいが望ましいといわれています。この推奨値の範囲内で収まるようにゲート断面積を決定します。
9:ゲート位置、レイアウトの決定
溶湯を金型に流入するゲートの位置を決定します。ダイカストの品質に大きく影響を与えるため、製品の機能、特性を十分に理解した上で金型の構造、鋳造方法、鋳造条件などを加味して決定する必要があります。
10:ランナー形状の決定
ランナーはスリーブまたはノズルからゲートへ溶湯を導く通路のことです。溶湯の金型内部への流入方向を決定します。
11:オーバーフロー、エアベントの決定
オーバーフローは、金型に巻き込まれたガスや温度の低下した溶湯、酸化物などを移動させる最終充填部のことです。また、エアベントは、スリーブやノズル、ランナー、金型内部のガスを排気する部位のことです。これらのガスが抜けないと欠陥の原因となる為、非常に重要な役割を持っています。
12:コンピュータによる解析・検証
コンピュータにより湯流れ解析や凝固解析などの検証を行います。湯流れ解析は、設定したランナー、ゲート、オーバーフローでの湯流れの判定や、ガスの巻き込みの不具合について検証を行います。凝固解析は、凝固遅れによるひけ巣の発生予測について検証を行います。
13:鋳造方案図完成
全ての関連部門で持っている知識を出し合って協議し、全部門の承認が得られたもので完成として運用することが必要です。
ダイカストの製品事例
充電器用ダイカストケース
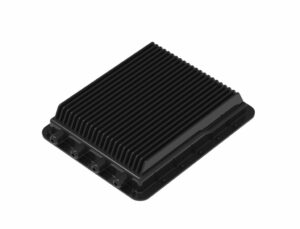
こちらは二輪やドローン、セニアカーなどの輸送機器に用いられる充電器用のケースです。
課題として、800t成形機を保有しているダイカストメーカーが少ないことが挙げられました。そのため、当社が提携している100社以上の協力会社の中から対応できるメーカーを選定して対応いたしました。
ダイカストのことなら、ダイカスト加工センターにお任せください!
こちらの記事では、鋳造方案設計についてご紹介いたしました。
当社では、国内外の自動車部品や住宅設備メーカー様向けに、ダイカスト品を納入してきた実績を基に、最適な材料選定や、ダイカストへの工法転換など様々な提案を行っております。アルミのみならず、亜鉛とマグネシウムのダイカストにも対応可能です。
ダイカストに関して、お困りごとがございましたら、お気軽にご相談ください。
最後までお読みいただき、ありがとうございました!